Введение
МЕТАЛЛОГРАФИЯ — это научная дисциплина, изучающая и определяющая состав и базовую
структуру (или пространственные отношения между) составляющих металлов, сплавов и материалов
(иногда называемая материалографией).
Исследование структуры может проводиться в широком диапазоне масштабов длины или уровней увеличения, начиная от визуального или малоувеличенного (~20×) исследования и заканчивая увеличением более 1 000 000× с помощью электронных микроскопов. Металлография также может включать изучение кристаллической структуры с помощью таких методов, как рентгеновская дифракция. Однако наиболее привычным инструментом металлографии является световой микроскоп с увеличением от ~50 до 1000× и способностью разрешать микроструктурные особенности размером ~0,2 мкм и более.
Другим основным инструментом исследования в металлографии является растровый электронный
микроскоп (РЭМ). По сравнению со световым микроскопом, СЭМ расширяет диапазон разрешения
более чем на два порядка до примерно 4 нм в обычных приборах, с предельными значениями ниже 1
нм. Полезное увеличение охватывает диапазон от стереомикроскопа, всего диапазона светового
микроскопа до большей части диапазона просвечивающего электронного микроскопа (ПЭМ) с
возможным увеличением от 1 000× до >100 000×. SEM также обеспечивает большую глубину резкости,
чем световой микроскоп, с глубиной фокуса от 1 мкм при 10 000× до 2 мм при 10×, что больше более
чем на два порядка по сравнению со световым микроскопом (табл. 1). Такая большая глубина резкости
позволяет лучше различать особенности топологии при микроскопическом исследовании, например,
при изучении поверхности трещины во время анализа разрушения. Глубина резкости РЭМ также может
быть фактором выбора по сравнению со световой макроскопией, когда на макроскопическом уровне
исследуются очень шероховатые поверхности. Дополнительную информацию о сравнительных
возможностях световой и электронной микроскопии см. в статье «Световая и электронная микроскопия»
в этом томе.
Однако даже с появлением электронной микроскопии световой микроскоп по прежнему остается
первым и самым важным прибором для исследования в металлографии. Иногда контрастность
микроструктуры недостаточна при использовании РЭМ с разрешением менее 500×, в то время как она
хорошо видна при использовании базового светового микроскопа и правильно подготовленного
образца. Действительно, световая микроскопия является историческим и практическим краеугольным
камнем металлографии, как описано в следующем разделе «Истоки металлографии», где кратко
изложено основное открытие Сорби, демонстрирующее важность подготовки образцов при
исследовании металлов с помощью светового микроскопа. Контраст между микроструктурными
составляющими при световой микроскопии очень зависит от подготовки образца. Световые
микроскопы также имеют различные виды специальных режимов освещения, которые позволяют увеличить информацию, получаемую из изображения (см. статью «Световая микроскопия» в этом томе). Например, освещение поляризованным светом позволяет улучшить фазовый контраст, а метод дифференциального
интерференционного контраста (ДИК) может быть использован для выявления топологических
перепадов высоты на поверхности образца размером менее 0,2 мкм.
Цель этих инструментов — точное выявление структуры материала на поверхности образца и/или на его
поперечном срезе. Исследование может проводиться на макроскопическом, мезоскопическом и/или
микроскопическом уровнях. Например, поперечные сечения, вырезанные из компонента или образца,
могут быть макроскопически исследованы с помощью светового освещения, чтобы выявить различные
важные макроструктурные особенности (порядка 1 мм — 1 м), такие как:
- Линии течения в кованых изделиях
- Структуры затвердевания в литых изделиях
- Характеристики сварного шва, включая глубину проплавления, размер зоны сплавления и
количество проходов, р а з м е р зоны термического влияния, а также тип и плотность дефектов
сварного шва - Общий размер и распределение крупных включений и стрингеров
- Дефекты изготовления, такие как нахлесты, холодные сварные швы, складки и швы в кованых
изделиях - Газовая и усадочная пористость в литых изделиях
- Глубина и равномерность упрочненного слоя в закаленном изделии
Макроскопическое исследование поверхности детали также необходимо для оценки состояния
материала или причины отказа. Оно может включать в себя:
- Характеристика макроструктурных особенностей поверхностей трещин для выявления места
зарождения трещины и изменений в процессе распространения трещины - Оценка шероховатости поверхности, шаблонов шлифования и углов хонингования
- Оценка целостности и однородности покрытия
- Определение степени и места износа
- Оценка пластической деформации, связанной с различными механическими процессами
- Определение степени и формы коррозионного воздействия; легко различимые типы воздействия
включают точечную, равномерную, щелевую и эрозионную коррозию - Оценка склонности к окислению
- Ассоциация отказов со сварными швами, припоями и другими технологическими операциями
Этот перечень макроструктурных признаков при характеристике металлов, хотя и неполный,
представляет широкое разнообразие признаков, которые можно оценить с помощью световой
макроскопии.
Мезомасштабная структура имеет размер от 1 мм до 100 мкм. Она включает в себя микроструктурные
особенности на уровне зерен, не позволяя разобраться в тонкостях зерновой структуры. Например,
однородность глубины корпуса является примером мезомасштабной особенности. Структуры
затвердевания на мезомасштабном уровне включают такие характеристики, как размер ячеек
(эвтектическая ячейка), дендриты и рукава, тип зерна (столбчатое или равноосное), тип и концентрация
химической микросегрегации, а также количество микроусадок, пористости и включений. Термин
«мезомасштаб» — относительно новый термин, введенный отчасти для более точного разграничения
различных масштабов.
Микроструктура — это классический термин, используемый в металлографии для описания
особенностей, наблюдаемых под микроскопом в диапазоне масштабов 1000-0,1 мкм. Важность
микроструктуры для свойств металлов и сплавов была признана давно. Размер зерна, двойники, а также
размер, форма и распределение частиц второй фазы играют важную роль в определении поведения
большинства металлов и сплавов. Эти микроструктурные особенности находятся в пределах
фундаментального разрешения света 0,2 мкм (или больше). Затем, при необходимости, исследование
может перейти на более высокие уровни увеличения с помощью сканирующего электронного
микроскопа или просвечивающего электронного микроскопа (ПЭМ). Например, дислокации,
многочисленные типы частиц второй фазы, спинодальные и упорядоченные структуры, а также многие
аспекты мартенситных структур слишком малы для разрешения с помощью световой микроскопии.
Поэтому металлографическое наблюдение этих очень тонких структурных особенностей обычно
ограничивается электронной микроскопией.
Истоки металлографии
Критическим фактором в световой микроскопии металлов является подготовка поверхности образца.
Это основная идея, открытая отцом металлографии Генри Клифтоном Сорби (рис. 1), который в 1863
году первым рассмотрел под микроскопом правильно отполированные и химически протравленные
металлические образцы (ссылка 1). Это применение микроскопии появилось более чем на два столетия
позже, чем биологический микроскоп, поскольку микроскопия металлов требует тщательной
подготовки поверхности. В отличие от биологических образцов, металлы непрозрачны и поэтому
требуют микроскопии в отраженном свете (когда падающий свет для просмотра отражается от
поверхности образца). Биологические образцы, напротив, прозрачны, поэтому их можно исследовать в
проходящем свете (просвечивающая микроскопия). Сорби понял необходимость правильной
подготовки поверхности при исследовании металлов с п о м о щ ь ю микроскопии отраженного света.
До Сорби образцы представляли собой лишь «искаженные изломы и грубо обожженные или абразивные
поверхности» (ссылка 2). Он советовал, что «(окончательная) полировка должна быть не такой, которая
дает яркое отражение, а такой, которая может показать все неровности материала и как можно дальше
от полированной поверхности» (ссылка 3).
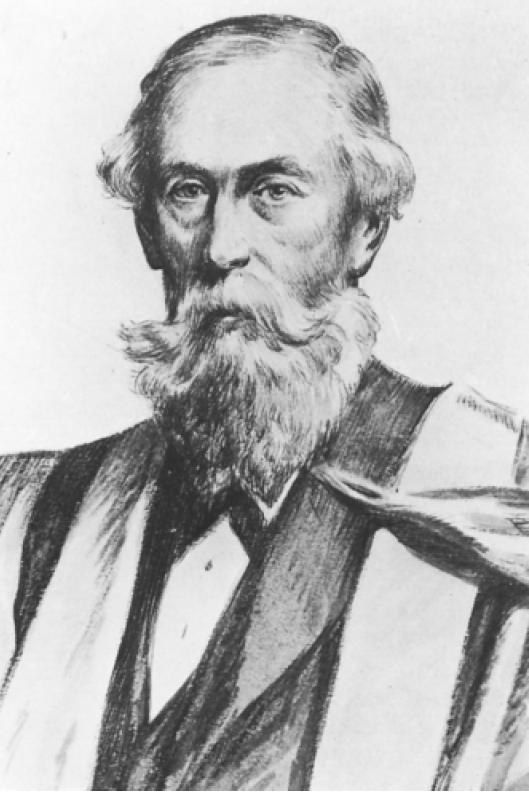
металлографии.
Другой частью металлографической головоломки является искусство травления. Чрезвычайно гладкая
поверхность кажется почти бесцветной при исследовании с помощью микроскопии отраженного света,
потому что свет равномерно отражается от поверхности и воспринимается человеческим глазом как однородный контраст. Поэтому необходимы методы усиления контрастных различий между разными фазами компонентов. К таким методам относятся травление, формирование тонких пленок или специальные режимы освещения в световых микроскопах (см. статью «Усиление контраста и травление» в этом томе). Химические рецепты травления поверхности являются самыми старыми среди различных методов контрастирования. Травление даже предшествовало Сорби, по крайней мере, на четыре столетия, как в случае с техникой макротравления для выявления дамасских узоров на мечах и различных предметах доспехов. Макротравление также использовалось для выявления структуры полированных метеоритов, например, знаменитой структуры Видманштеттена, обнаруженной графом Алосом фон Видманштеттеном, геологом и хранителем музея в Вене, и его коллегой Карлом фон Шрайберсом в 1808 году. Они протравили различные метеориты, чтобы показать выдающиеся кристаллические узоры в железном метеорите Эльбоген, упавшем в 1751 году. Прекрасный пример их работы показан на рис. 2.
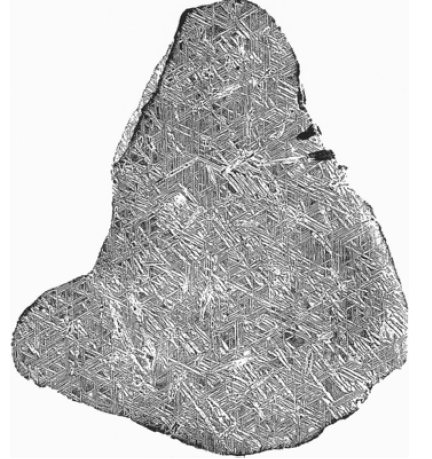
и Шрайберсом методом сильного травления в азотной кислоте. После промывки в воде и сушки
на протравленную поверхность наносилась типографская краска, и образец прижимался к листу
бумаги.
Видманштеттен и Шрайберс вытравливали образцы, которые можно было рассмотреть невооруженным
глазом, но Сорби был первым, кто вытравил образцы и наблюдал истинную микроструктуру с помощью
микроскопа. Сначала Сорби разрезал и полировал образцы, чтобы удалить все «следы шероховатости».
После полировки он использовал чрезвычайно разбавленную азотную кислоту для травления образцов.
Он следил за ходом травления, чтобы не перетравить образец. Критическим фактором в этой процедуре
была кропотливая подготовка образцов, которую Сорби проводил вручную. Полированные поверхности
были протравлены в разбавленном азоте и, несомненно, были значительно выше, чем у его
современников, таких как Веддинг и Мартинс в Германии (ссылка 5), которые также пытались выявить
микроструктуру сталей.
Возможно, Сорби не осознавал точных причин успеха своих методов приготовления, но важнее то, что
все структуры, о которых сообщал Сорби, до сих пор считаются правильными. 28 июля 1863 года
Сорби записал в своем дневнике, что он «открыл» структуру железа. Однако только в 1886 и 1887 годах
его результаты были опубликованы в журнале с широкой читательской аудиторией (Ref 1, 3). Путем
тщательного наблюдения он определил основные микроструктурные составляющие материалов из
черных металлов (составляющие, известные сегодня как графит, цементит, перлит, аустенит* и
фосфидная эвтектика). Он понял, что железо состоит из множества кристаллических зерен, а также
осознал, что при нагревании железо претерпевает аллотропические изменения. Как отмечает Сэмюэлс
(ссылка 6), это потрясающие достижения, учитывая, что он начал с нуля и что они были достигнуты за
такой короткий период исследований.
С этого момента важность подготовки образцов остается главной и сегодня. Многие недостатки
возникают, если пренебречь методами подготовки. Ложные структуры (или артефакты) могут возникать
в результате подготовки различными способами. В частности, Хосе Рамон Вилелла (рис. 3) первым
понял, что артефакты иногда наблюдаются из-за наличия слоя «искаженного или нарушенного»
металла, образовавшегося на ранних стадиях подготовки поверхности, а не во время самой полировки
(ссылка 7)1. Он показал, что истинная микроструктура видна только при удалении нарушенного слоя, и
разработал метод (попеременное травление и полировка), позволяющий это сделать (рис. 4)
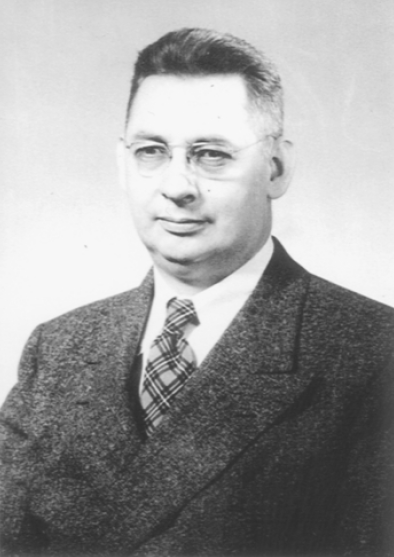
необходимость точной подготовки репрезентативных поверхностей при металлографических
исследованиях.
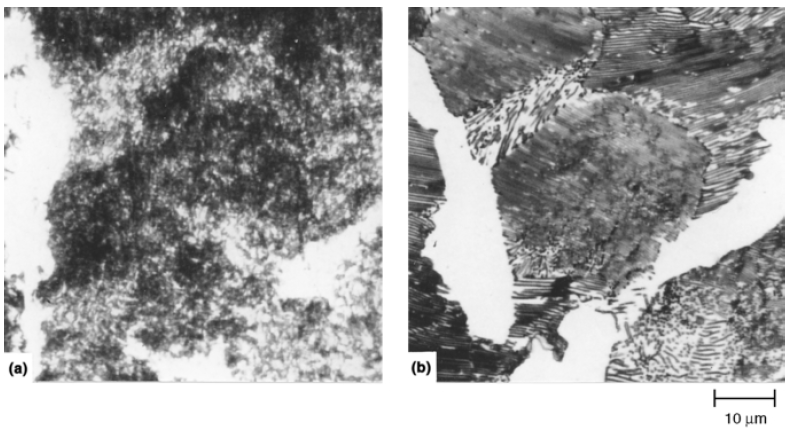
внешний вид перлита.
(a) Полированная поверхность, покрытая слоем нарушенного металла; структуры такого типа
некоторые ранние исследователи называли сорбитом или троостит-сорбитом. (b) То же поле после
удаления слоя нарушенного металла путем попеременной полировки и травления; истинная
структура пластинчатого перлита. Травление в пикральном реактиве. 1000×
Основополагающая работа Вилеллы определила необходимость подготовительных процедур,
выходящих за рамки простого получения отражающих поверхностей. Успешная металлография
предъявляет следующие требования к окончательной подготовке поверхности образца (Ref 6):
- Поверхностные слои, которые могут заслонить структурные особенности, не должны
присутствовать. - Ложные структуры, которые могут быть обнаружены при последующем обследовании, не должны
быть введены. - Все желаемые поля зрения должны быть компланарными в пределах глубины резкости системы,
которая будет использоваться для исследования. - На поверхности не должно быть пятен и других случайных дефектов.
Учитывая эти основные цели, следующим вопросом является определение наиболее эффективных
механических, химических и/или физических методов подготовки образцов для соответствующего
микроскопического инструмента.
После получения и регистрации микрофотографии правильно подготовленного образца следующей
задачей является интерпретация, понимание и использование информации, содержащейся в записанном
изображении. Интерпретация микроструктурных особенностей требует понимания кристаллической
структуры, кинетики и металлургических механизмов затвердевания, деформации и фазовых
превращений. Интерпретация микрофотографий также требует понимания того, как подготовка образцов и микроскопические методы влияют на внешний вид определенных фаз в данном материале. Таким образом, каталогизация микрофотографий (в печатном и/или электронном виде) может быть полезна при сравнении влияния вариаций материала и изменений в подготовке образцов.
Сноска
В конце XIX века очень тонкий перлит, не разрешаемый в световых микроскопах, называли
«сорбитом» в честь Сорби. Однако, поскольку это не новый компонент, термин «сорбит» не
сохранился.
Термин «перлит» сохранился до наших дней и на самом деле связан с Сорби, потому что он описал
«перламутровую составляющую», то есть перлит, как имеющий вид «перламутра».
Ссылки, цитируемые в данном разделе
- Х.К. Сорби, в книге «Как работать с микроскопом», Лондон, 1867 г.
- К.С. Смит, История металлографии, Издательство Чикагского университета, 1960 г.
- H.C. Sorby, J. Iron Steel Inst., Vol 28, 1886, p 140
- Б.Л. Брамфитт и А.О. Бенскотер, Руководство для металлографов: Практика и процедуры для
железа и сталей, ASM International, 2002, стр. 88 - H. Wedding, J. Iron Steel Inst., Vol 27, 1885, p 187
- Л.Е. Сэмюэлс, Металлографическая полировка механическими средствами, 4-е издание, ASM
International, 2003, стр. 6 - J.R. Vilella, Металлографические методы для сталей, Американское общество металлов, 1938 г.
- J.R. Vilella, Металлографические методы для сталей, Американское общество металлов, 1938 г. ↩︎
Добавить комментарий